
BESPOKE KITCHEN CANOPY VENTILATION SYSTEMS
Sigma EPD design and install solid flue extract and bespoke kitchen canopy ventilation systems that remove exhaust gases from an appliance burning solid fuels (like wood or charcoal) and safely vents them outside. It's crucial for safety, ensuring dangerous gases don't build up indoors, and for the efficient operation of the solid fuel appliances.
Bespoke Kitchen Canopy Ventilation System for Scotts Seafront Restaurant, Greenock

Client: Buzzworks Holdings (Scotts Restaurant)
Sector: Hospitality
Services Provided: Custom Kitchen Canopy Design, Integrated Make-Up Air System, Aesthetic-Focused Engineering
About the Client
Scotts, part of the Buzzworks Holdings group, is an upscale bar and restaurant located on the Greenock seafront, offering panoramic views over the River Clyde. As part of its design ethos, the restaurant places a high priority on visual appeal, making it essential that all mechanical and structural installations, particularly in its open-plan kitchen, blend seamlessly with the elegant interior aesthetic.
Challenges:
Sigma Engineering Product Design Ltd was appointed by Blue Refrigeration to design and install a bespoke commercial kitchen canopy at Scotts. The restaurant’s open plan layout meant the entire system would be visible to diners, requiring a solution that was:
• Fully compliant with TR/19, DW/172, and DW/144 specifications
• Visually seamless, with no exposed fasteners or obvious structural supports
• Engineered to integrate a make-up air system that would wrap around the canopy without disrupting the interior aesthetic
The canopy had to span an area of 7.1m x 3.2m, accommodating a high-performance extraction system while maintaining architectural discretion.
Our Engineering Approach
1. Central Filter Section Reinvention
The conventional method of hanging the baffle filter from the canopy roof was unsuitable due to the size of the structure. It risked deforming the roof and compromising performance. Sigma’s solution:
• Reinforced the top of the filter housing, making it structurally stiff enough to carry both its own weight and that of the roof
• Integrated ceiling-suspended rods that passed through pre-cut holes in the assembly
• Used nuts and washers to securely suspend the central filter bank and form a sealed plenum, ensuring even airflow on extract
2. Roof Panel Engineering
​
The canopy roof was divided into twin panels positioned on either side of the central filter bank:
• Panels were designed with fabricated upstands for precise alignment and mechanical fixing to the filter section
• This eliminated the need for visible support brackets and maintained structural integrity
3. Side and Front Panel Integration
​
• Side and front panels were fabricated with hemmed sections to receive the roof edges
• This created a locking mechanism, allowing the roof panels to slot in and be secured discreetly from within
• The result was a smooth, cohesive structure, ideal for high-visibility restaurant environments
Make-Up Air Strategy
To prevent thermal discomfort and air stagnation in the kitchen, Sigma designed a dual direction make-up air system:
• Air was introduced horizontally across the kitchen to supply general ventilation
• Simultaneously, air was directed vertically downward at the canopy’s lip, improving airflow capture and maintaining temperature balance
• The system featured a custom-designed, removable ‘L’-shaped supply diffuser, which simply clipped into place for ease of maintenance and installation
The Outcome
Sigma EPD successfully delivered a high-performance, aesthetically refined canopy system tailored to the specific visual and functional demands of Scotts in Greenock. The result:
• A structurally robust, visually seamless canopy system
• Integrated dual-function make-up air delivery for thermal comfort and efficient extraction
• Compliance with all industry regulations while maintaining architectural harmony with the restaurant's luxury design
This project stands as an example of engineering excellence meeting high-end design, supporting both staff performance and customer experience in a visible, openplan kitchen setting.
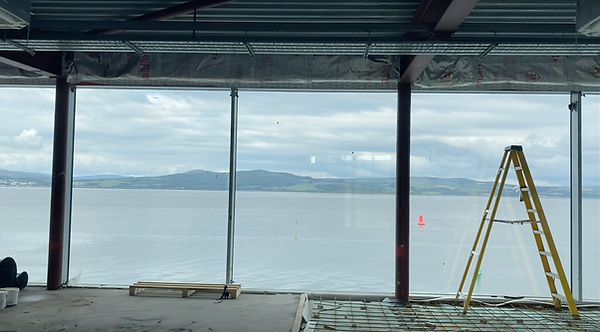
Ventilation of New Brown Brothers Factory – Energy-Efficient Climate Control for Large-Scale Food Production

Client: Brown Brothers, Kirkconnell
Sector: Food Production
Services Provided: Ventilation Design, Air Quality Engineering, Custom Diffuser Systems
About the Client
Brown Brothers is a renowned producer of cooked meats based in Kirkconnell, Scotland. The company supplies many well-known brands such as Greggs, M&S, and Waitrose. As part of a new facility expansion, the client sought a cutting-edge ventilation solution that would meet strict temperature and air change requirements while maintaining energy efficiency.
Challenges:
In November 2022, Sigma EPD was approached to evaluate and deliver a ventilation solution for the low-risk production area of Brown Brothers’ new-build factory; a space over 115 meters in length.
Key performance requirements included:
​
• Maintaining an ambient temperature of 3°C
• Delivering 2 Air Changes per Hour (ACH) across the large internal space
Conventional ventilation proposals involved replacing the entire air volume twice per hour and cooling incoming air from ambient to 3°C. An approach that carried prohibitively high energy costs.
Our Engineering Approach
Sigma EPD proposed a more energy-efficient, advanced alternative using the newly launched Sigma360 Filtration Ventilation System (FVS).
1. Advanced Air Filtration with Heat Recovery
• Sigma360 captures and recycles stale indoor air by passing it through a dual filtration system including pre-filters and H14 HEPA filters, while simultaneously filtering incoming outdoor air.
• The system retains nearly 100% of the heating/cooling energy already present in the air, drastically reducing energy demand.
• Air volumes from internal and external sources are mixed, improving indoor air quality and maintaining target conditions.
2. High-Efficiency Fan and Control Systems
​
• Electronically Commutated (EC) fans ensure minimal energy consumption and optimal airflow.
• Each fan unit is controlled by a UNIcon (CPG) system to regulate pressure and maintain constant volume flow.
• Temperature control integration provides additional efficiency in managing air quality.
3. Bespoke Stainless Steel Diffusion System
​
To effectively manage airflow in the expansive space:
​
• A custom stainless-steel eyeball diffuser system was designed to distribute air across large distances.
• Air is returned through strategically placed extract grilles, facilitating efficient recirculation.
• The diffuser system was precision-cut using in-house water jet machinery from DXF files generated in our 3D CAD modelling system, allowing for efficient, repeatable manufacture of complex geometries.
• Cleanout access ports were integrated into each plenum to enable easy maintenance.
Overcoming Installation Challenges
Due to the large size of the filtration units:
​
• Significant coordination was required to lift and secure equipment to the roof structure.
• Fire dampers were installed wherever the system penetrated fire curtains, in line with BSB Ltd. specifications.
• Each fire damper installation included inspection access doors to ensure maintainability and compliance with fire safety standards.
The Outcome
Sigma EPD delivered a high-performance, low-energy ventilation solution tailored to the demands of large-scale food manufacturing. The Sigma360 system provided:
• Reliable temperature control with minimal energy cost
• Enhanced air quality via H14 filtration
• Full compliance with hygiene, fire safety, and operational standards
Brown Brothers benefited from a solution that not only reduced energy bills but also enhanced operational control, all while aligning with the company’s focus on quality and sustainability.
Atria One – Engineering Safer, Smarter Ventilation

Client: Atria One, Edinburgh
Sector: Commercial Offices
Services Provided: Engineering Consultancy, Risk Assessment, Custom Ventilation System Design & Installation
About the Client
Atria One is a premier Grade A office development located in the heart of Edinburgh’s city centre. Known for its contemporary architecture and commitment to sustainability, the building accommodates leading businesses and government agencies. Its flexible, high-spec office spaces are underpinned by cutting-edge energy performance features. Sigma EPD was approached to support the building’s ongoing commitment to performance efficiency through a complex ventilation system retrofit.
Challenges:
Sigma EPD was commissioned to evaluate and enhance the building’s ventilation infrastructure. However, significant issues arose due to the original ducting’s poor support system, which posed structural and operational risks.
​
Key challenges included:
​
• Inadequate support of existing ducting, meaning temporary structural reinforcement to prevent collapse during removal and installation, was a necessity.
• Tight project scheduling, requiring full removal and reinstallation of ductwork every weekend to ensure full operational service during weekdays.
• Spatial constraints, with minimal clearance between supply and extract ducts and limited access near walls.
• Safety risks, especially across a seven-floor riser, where personnel access was required.
Our Engineering Approach
Sigma EPD developed a bespoke design combining structural adaptation, custom component fabrication, and a phased installation strategy:
1. Structural Support and Safety Engineering
A dual-level support strategy was implemented: upper and lower ducts were secured using stainless-steel wire ropes with clutches, enabling incremental load adjustment in real time.
Beam clamps and threaded rods provided vertical support, with access holes cut into the ducts for fastening.
To prevent slippage, ducts were tethered to structural floor members using cleats and custom fabricated brackets designed in-house.
2. Custom Ducting Solutions
​
Due to tight wall clearance, internal flanges were fabricated and bolted from inside the duct, with erectors working within confined sections from the top down. A pulley suspension system was designed to safely lift and position duct sections during installation.
3. Enabling Access & Installation
​
Lightweight but rigid metal covers were designed and manufactured to span open ductwork. These covers allowed operatives to walk safely over the open ducts and enabled sca6olding installation at three meters above floor level.
This made it possible to install ducting efficiently and safely across seven floors, from the ceiling level down to the ground floor.
​
​
The Outcome
Sigma EPD successfully delivered to the constraints and specifications of Atria One. The final installation contributed significantly to Atria One’s BREEAM "Excellent" rating, improving indoor air quality and reducing long-term energy costs. Sigma’s innovative and safety first approach ensured minimal disruption to building operations, delivering a technically complex solution on time and in full compliance with building and safety standards.

GOT A QUESTION ABOUT OUR PROJECTS?
For bespoke kitchen canopy ventilation systems in Irvine, contact us. We are happy to answer any questions about our solid flue project or anything else, just give us a call.
CALL US: 01294 620031
EMAIL US: info@sigmaepd.com